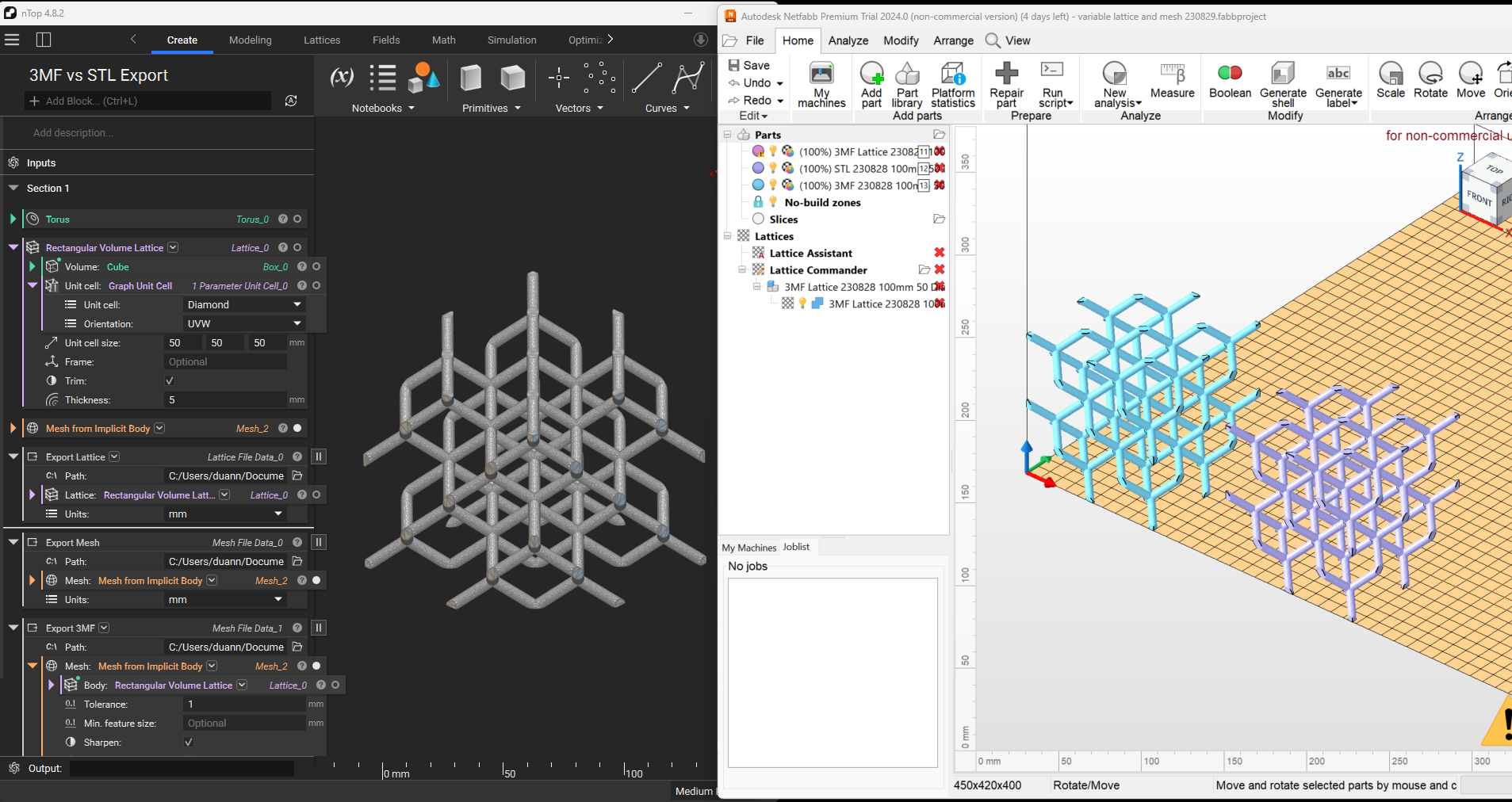
Dramatically Reduce File Size with .3mf Beam Lattice Extension
- Reduction in File Size
- Zero Loss of Resolution
- Lightweight Design AND File at the Same Time
The utilization of the 3MF Beam Lattice extension offers distinct advantages in the realm of additive manufacturing and computational design. First and foremost, it provides a highly efficient means to represent complex lattice structures, which are integral in applications such as material optimization, thermal management, and lightweighting. By using beams to describe these structures instead of traditional mesh elements, the extension significantly reduces file sizes. This leads to faster data transfer rates and more efficient storage, thereby streamlining the entire manufacturing workflow.
Moreover, the reduced computational load accelerates slicing processes, allowing for quicker transitions from design to production. Additionally, the Beam Lattice extension is designed to be seamlessly integrated into existing 3MF workflows, ensuring that there is no need for a radical overhaul of current processes or systems.
What is the 3mf Beam Lattice Extension?
The 3MF Beam Lattice extension is a specialized feature within the 3MF file format, designed to optimize the representation of lattice structures in additive manufacturing. This extension provides a more efficient way to describe complex lattice geometries, which are often used in lightweighting, material optimization, and thermal management applications. By utilizing beams instead of mesh elements to represent the lattice, the Beam Lattice extension significantly reduces file size and computational load. This enables faster data transfer, streamlined slicing processes, and ultimately, more efficient additive manufacturing workflows. The extension is particularly beneficial for industries like aerospace, automotive, and medical devices, where intricate lattice structures are commonly employed for their unique mechanical properties.
Problems with Representing Lattice Structures with Mesh Representation
Exporting lattice structures in a mesh format can lead to rapidly escalating file sizes, as the number of triangles required to accurately represent the geometry increases exponentially with the complexity of the lattice. This not only burdens data storage and transfer but also extends the computational time for slicing and simulation processes. Additionally, the increased mesh size introduces a greater likelihood of loss of fidelity in the geometric representation. This can result in increased errors in the mesh, such as inconsistencies and artifacts, which could compromise the structural integrity and functional performance of the final manufactured part. Therefore, the limitations of mesh formats for complex lattice structures can introduce inefficiencies and risks in additive manufacturing workflows.
Comparing .3mf Beam Lattice to .stl & .3mf Mesh Representation
In a practical example to demonstrate the efficacy of the .3MF Beam Lattice extension, consider a 100mm cube that is initially meshed and then subjected to an increasingly intricate ‘Diamond’ cell lattice structure. Starting with a 50mm cell size, a 5mm strut thickness, and a 1mm mesh tolerance, the complexity is incrementally increased to a 2mm cell size with a 0.5mm mesh tolerance. In this scenario, the mesh representation experiences a dramatic increase in file size and processing time due to the escalating complexity of the lattice. Conversely, the .3MF Beam Lattice representation remains compact and manageable, maintaining its original file size without compromising on resolution or accuracy. This stark contrast underscores the efficiency and reliability of the .3MF Beam Lattice extension, especially when dealing with complex geometries that would otherwise be cumbersome to handle using traditional mesh formats.
Meshing a Simple Cube
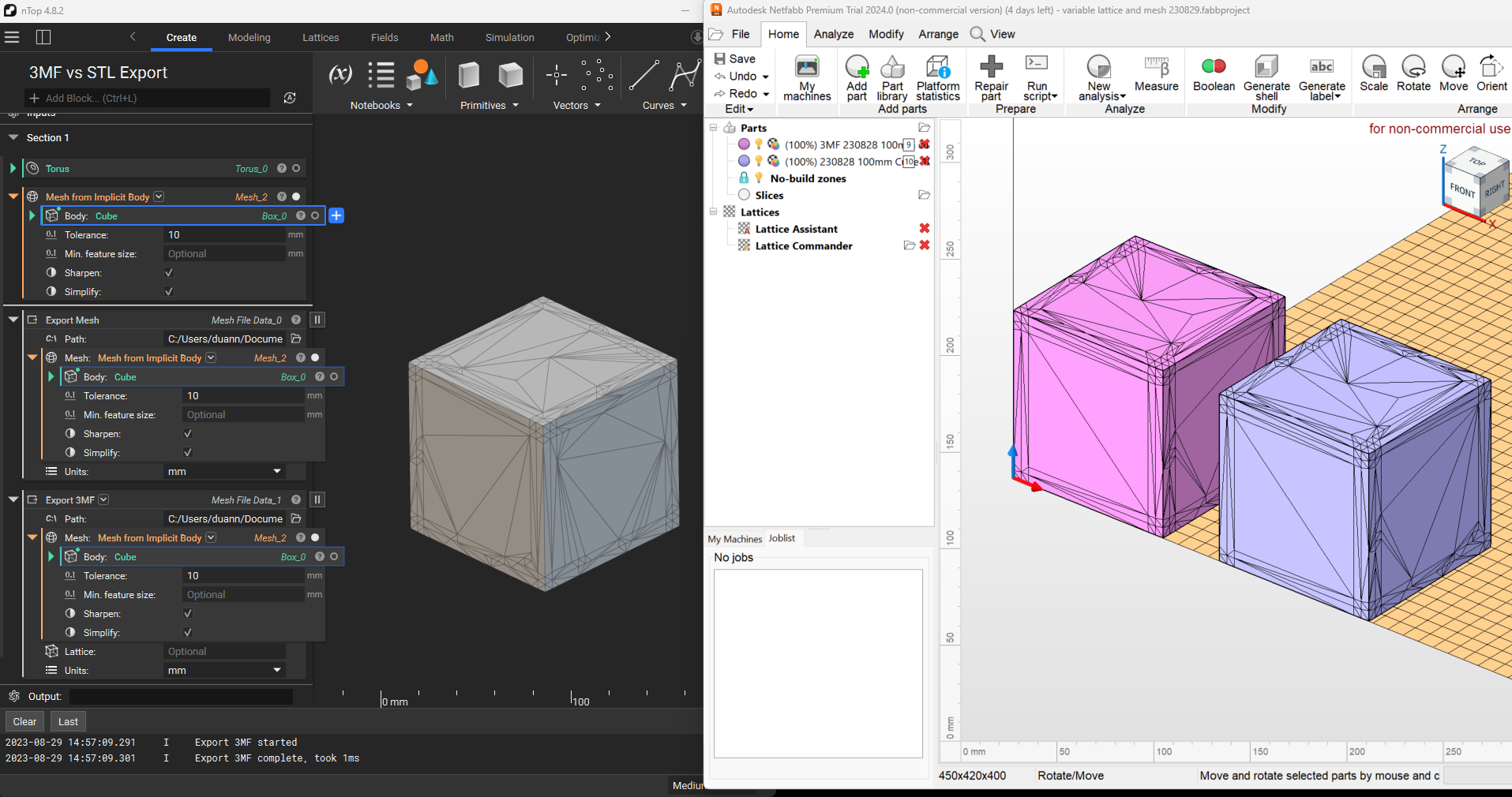
In this experiment, we begin by meshing a straightforward cube.
Although the meshing algorithm employed is not optimized for efficiency, it serves as a baseline for a like-for-like comparison as we introduce more complex lattice structures. In this initial stage, the .STL file size stands at 2344kb, while its .3MF counterpart is considerably smaller at 520kb. This already shows a significant difference in file sizes, with the .3MF file being approximately 78% smaller than the .STL file.
As we proceed to add more intricate geometries, this disparity becomes even more pronounced, highlighting the advantages of using the .3MF Beam Lattice extension for complex structures.
Comparing a Simple Lattice Structure
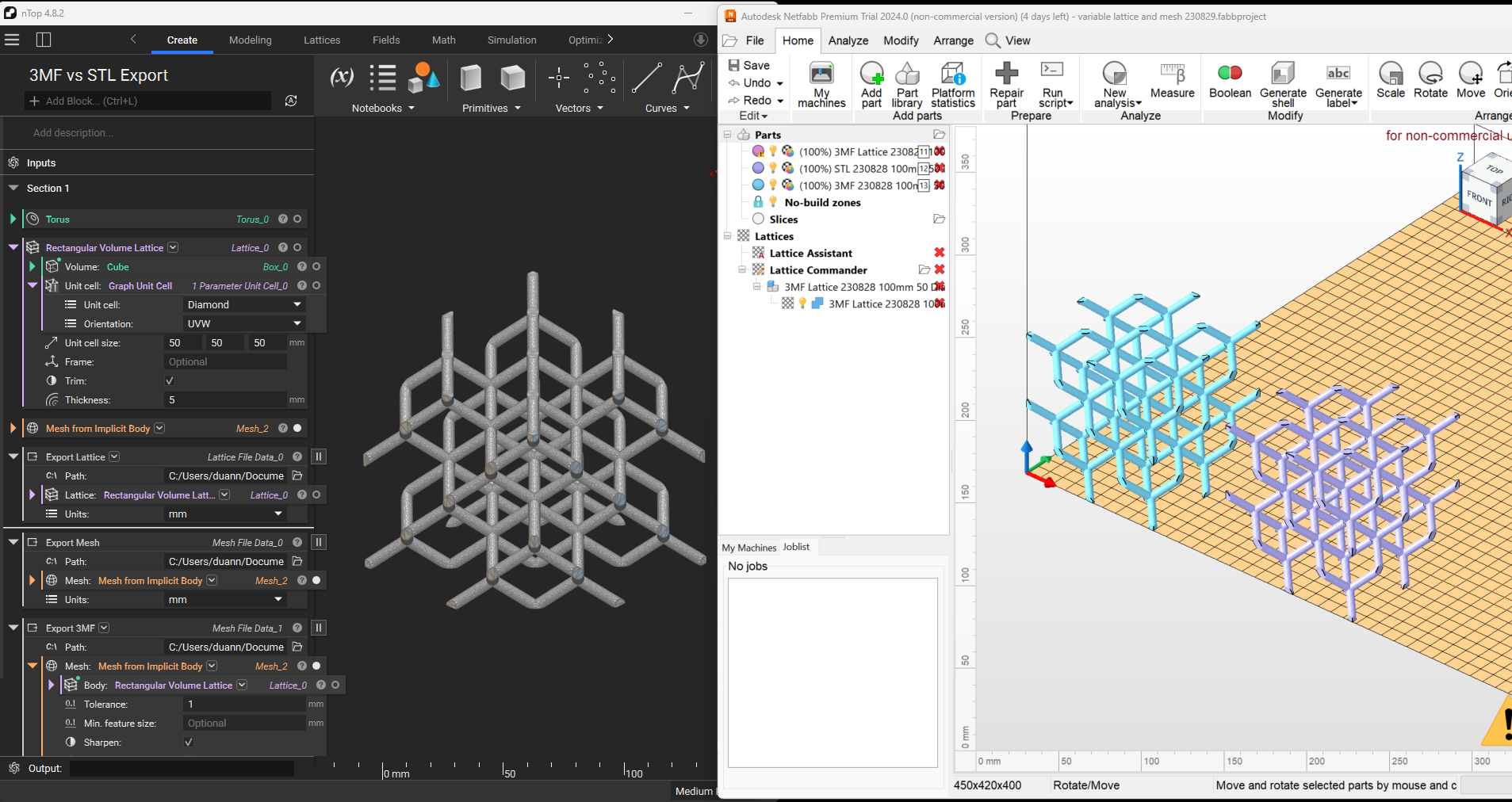
Upon introducing the first simple diamond lattice structure featuring a 50mm Diamond Unit Cell with a 5mm thick strut, the disparity in file sizes becomes even more evident. The STL mesh file size increases to 2467kb, while the identical mesh in .3MF format is considerably smaller at 800kb. Most notably, the .3MF Beam Lattice representation is a mere 3kb.
This represents a staggering 99.9% reduction in file size compared to the STL mesh.
The data clearly illustrates the efficiency of the .3MF Beam Lattice extension, especially when dealing with lattice structures, where it maintains high geometric fidelity at a fraction of the file size.
How Does the .3mf Beam Extension Work?
This remarkable reduction in file size is possible because the .3MF Beam Lattice extension represents the lattice structure as a series of beams connecting nodes, rather than as a mesh of interconnected triangles. Each beam is defined by its endpoints and cross-sectional properties, allowing for a highly compact yet accurate representation of the lattice geometry. This approach eliminates the need for numerous triangles to approximate the shape of each strut in the lattice, thereby drastically reducing the amount of data required to describe the same geometry. Consequently, the .3MF Beam Lattice extension enables a more efficient and manageable file size without sacrificing resolution or accuracy.
Increasing Lattice Complexity Without Sacrificing Accuracy
The .3MF Beam Lattice extension’s efficiency becomes even more apparent when increasing the complexity of the lattice structure. Reducing the Diamond cell size to 25mm while maintaining a 1mm resolution and 5mm strut thickness results in a substantial increase in the STL file size to 8417kb.
The equivalent mesh in .3MF format is smaller at 2706kb, but the Beam Lattice representation remains exceptionally compact at just 11kb.
Moreover, the meshing time for the STL file becomes a consideration, taking 6190ms, whereas the Beam Lattice generation is nearly instantaneous.
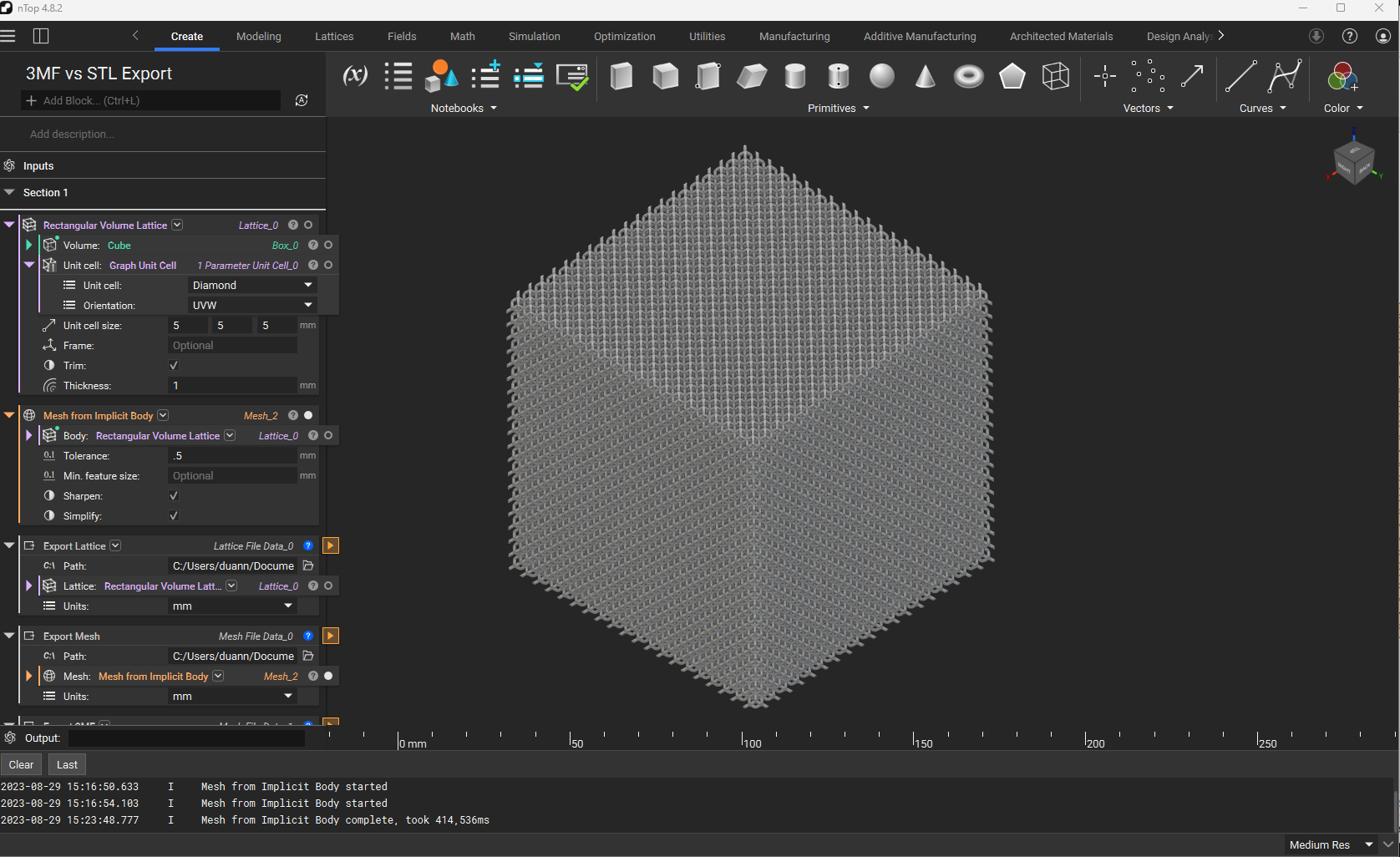
As we increase complexity, a 100mm cube with a 10mm Diamond cell size and a 1mm resolution, the file size and meshing time disparities become even more pronounced. The STL file size balloons to 22,882kb, while the equivalent .3MF mesh is 6,904kb. Remarkably, the .3MF Beam Lattice representation remains extremely compact at just 122kb.
The meshing time for the STL file takes a considerable 49,383ms, whereas the Beam Lattice is generated in a near-instantaneous 78ms. These figures underscore the .3MF Beam Lattice extension’s capability to handle highly complex lattice structures with unparalleled efficiency, both in terms of file size and processing time.
When the lattice complexity is pushed even further, reducing the Diamond cell size to 5mm with a 0.5mm resolution in a 100mm cube, the limitations of traditional formats become glaringly evident.
The STL file size increases to 181,416kb, while the corresponding .3MF mesh is 54,038kb. In stark contrast, the .3MF Beam Lattice representation remains manageable at 962kb.
Additionally, the meshing time for the STL file is notably high at 94,252ms with the lattice graph still taking only 78ms to produce and 19ms to export.
As the lattice complexity increases, the triangle count also becomes a significant factor, reaching as high as 468,602 triangles in this example. Such a high triangle count not only exacerbates the file size and processing time issues but also introduces the potential for errors within the mesh. These errors can be challenging to identify and time-consuming to rectify, further complicating the additive manufacturing workflow. The .3MF Beam Lattice extension, by reducing the need for such a high number of triangles, mitigates these risks and streamlines the process.
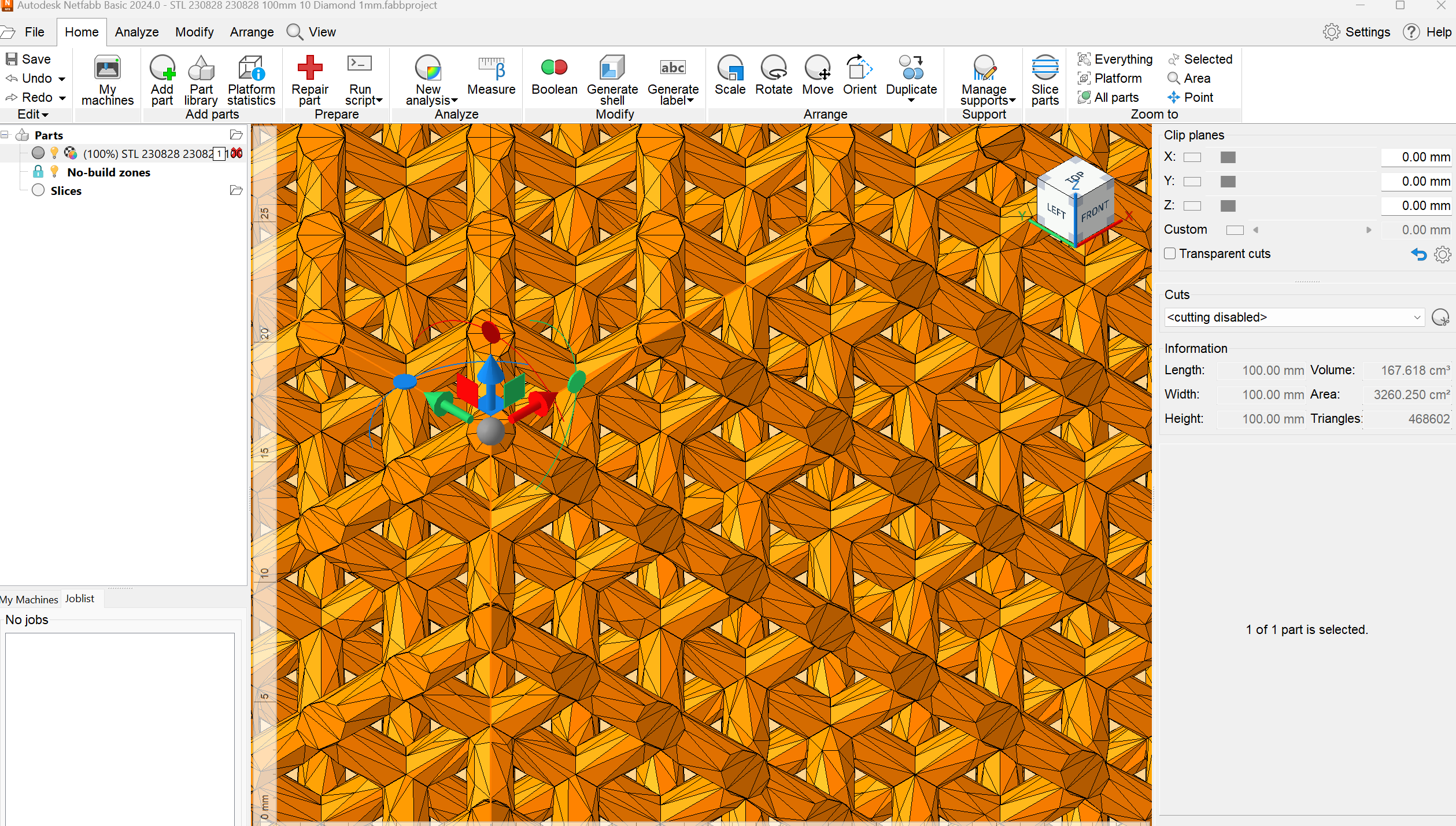
With Complexity, Meshing Becomes a Blocker to Productivity
“Beam lattice extension is a game changer.”
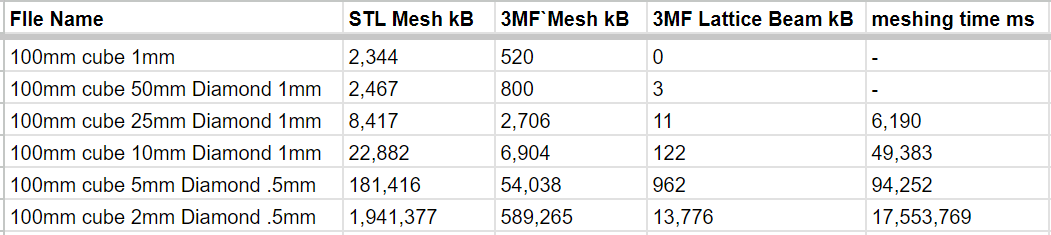
When the lattice structure is further refined to a 2mm Diamond cell size with a 0.5mm resolution within a 100mm cube, the limitations of traditional mesh formats become insurmountable. The STL file size reaches an unmanageable 1,941,377kb, and the corresponding .3MF mesh at 589,265kb. In contrast, the .3MF Beam Lattice representation remains relatively compact at 13,776kb. At this level of complexity, traditional mesh formats are not just inefficient; they become practically unusable. The .3MF Beam Lattice extension stands out as the only viable option for handling such intricate lattice structures in a manageable and efficient manner.
At this extreme level of complexity, meshing doesn’t just become inefficient—it turns into a significant blocker to productivity. The exorbitant meshing time of 17,553,769ms essentially halts the workflow, delaying subsequent stages of the design and manufacturing process.
This bottleneck can lead to missed deadlines and increased costs, undermining the overall efficiency and effectiveness of additive manufacturing operations. In contrast, the .3MF Beam Lattice extension, with its manageable file sizes and near-instantaneous processing times, allows for uninterrupted workflow, thereby maintaining productivity even when dealing with highly complex lattice structures.
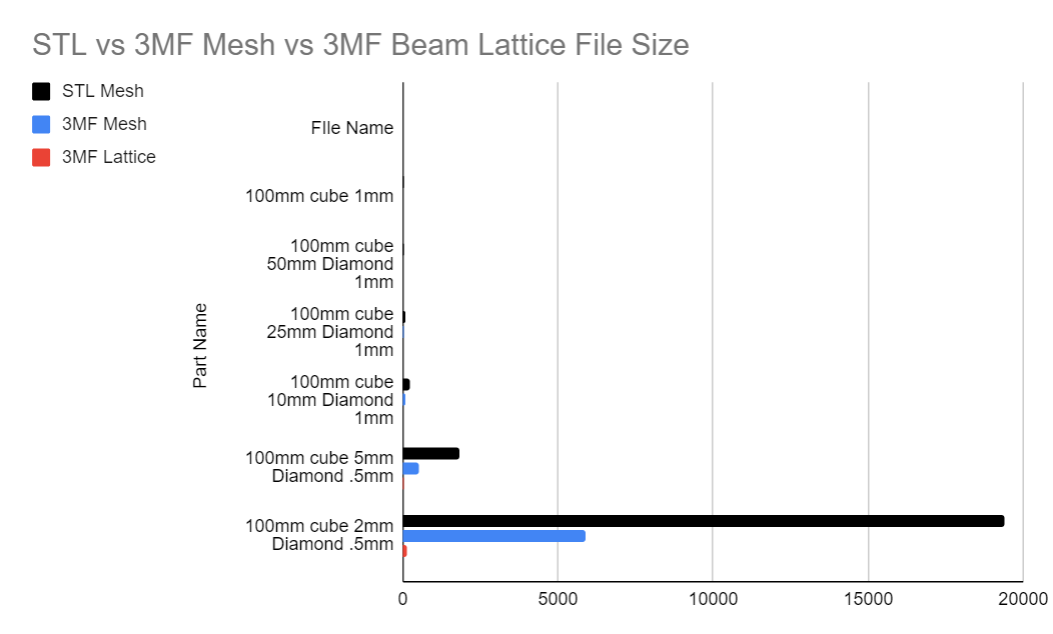
When examining the file sizes across STL, 3MF, and the Beam Lattice extension, the differences are so pronounced that the Beam Lattice’s footprint is almost negligible on the chart. This extreme divergence in file sizes will be clearly evident in the accompanying graph, highlighting the Beam Lattice extension as a remarkably efficient alternative for managing intricate lattice structures in additive manufacturing.
Start Using the .3mf Beam Extension for Complex Lattice Structures
Leading design and engineering software platforms already offer support for the .3MF Beam Lattice extension to export intricate lattice structures, such as Autodesk Fusion360, Siemens NX and nTop. Additionally, industrial AM slicing software like Magics and Netfabb natively support this extension, streamlining the transition from design to manufacturing.
To verify if your software is compatible with the .3MF Beam Lattice extension, consult the 3MF compatibility matrix. If your software is not yet supported, we encourage you to reach out to us, and we will collaborate with the software providers to facilitate its integration.
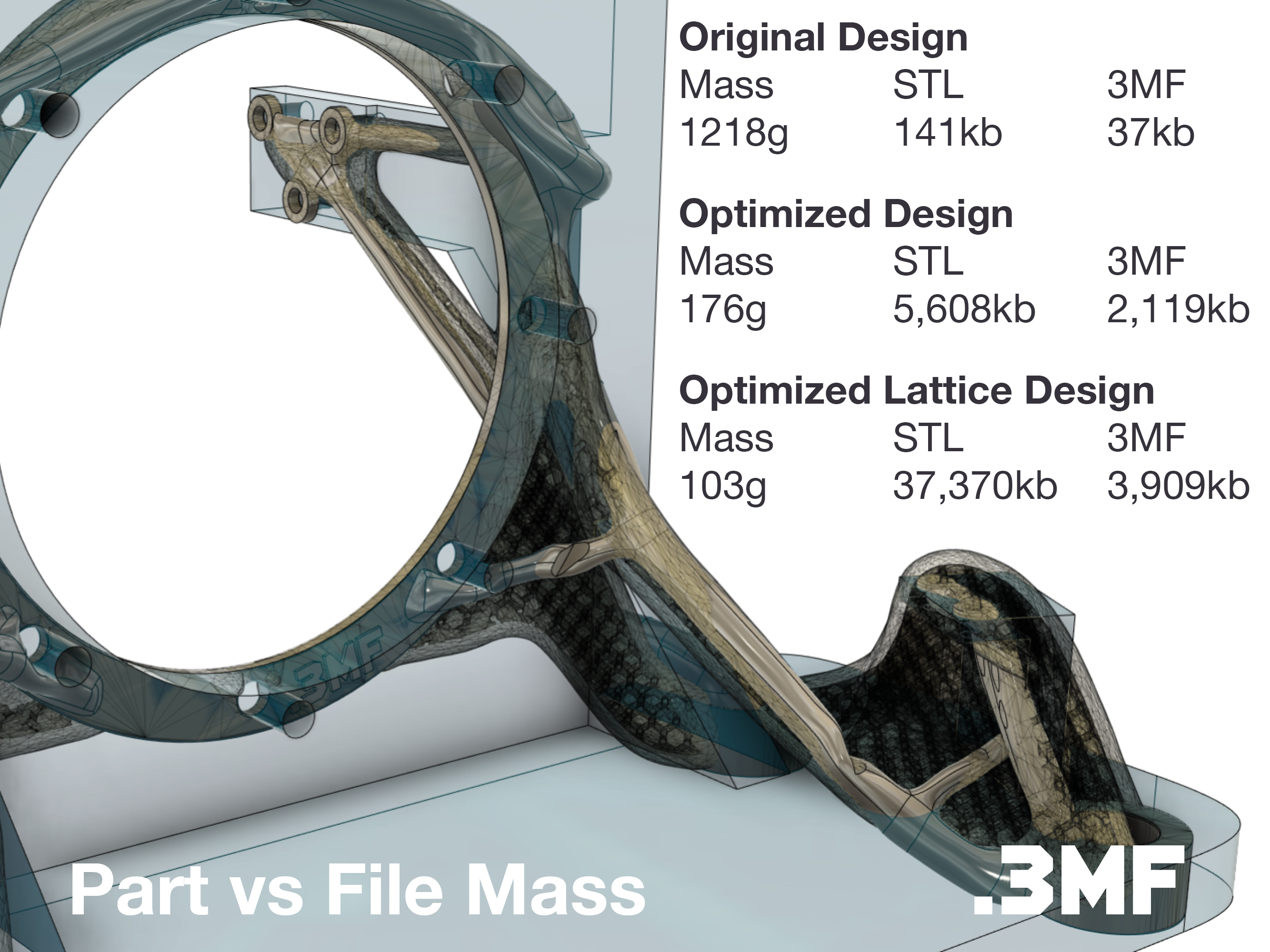